Energy usage
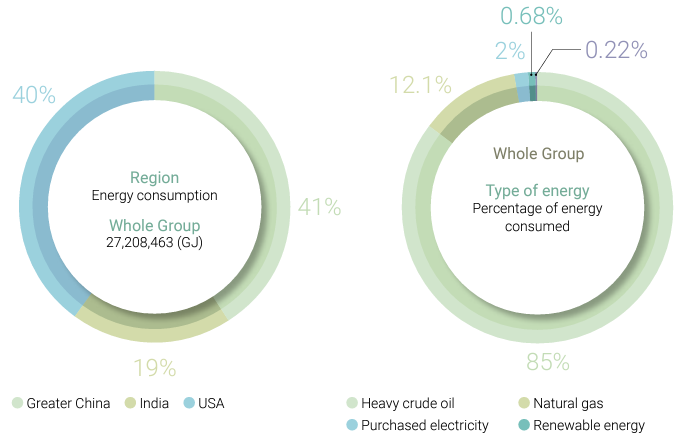
In the process of manufacturing carbon black, CSRC mainly uses heavy crude oil, purchased electricity, natural gas, diesel, self-produced electricity, and process waste gas. Some plants also use renewable energy. In 2023, the total internal energy consumption of the Group was 27,208,463 GJ, of which the plants in Greater China accounted for 41%, India 19%, and United States 40%. As the total carbon black output in 2023 is lower than that in 2022, and the improved process technology has directly led to significant reduction in the overall oil consumption of raw materials, energy consumption, and energy intensity. In 2023, the energy intensity of the Group was 78 GJ/metric ton, and the energy intensity of the plants in each region was 72 GJ/metric ton in Greater China, 74 GJ/metric ton in India, and 88 GJ/metric ton in the United States, respectively.
In 2023, the percentages of self-produced for self-use and the self-produced electricity for self-use by the plants in Greater China reached 53% and 84%, respectively; the percentages in India reached 90% and 29%, respectively; the percentages in the United States reached 100% and 65%, respectively; the groupwide percentages reached 65% and 62%, respectively.
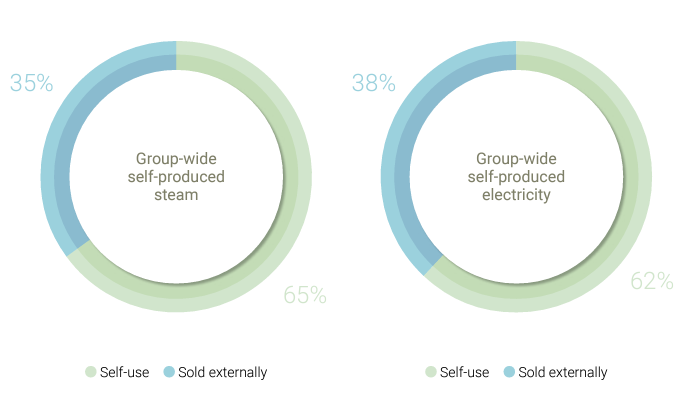
CSRC will continue to track each operating plant’s carbon black output, gas output and electricity consumption per ton of carbon black, power generated per unit of steam, boiler use status, and steam feedwater quality for energy use efficiency management, while repairing and maintaining equipment to ensure that the equipment is operating with high energy efficiency.
Energy consumption by plants in various regions over the past three years

Note 1 | There are two sources of process waste gas. One is the waste gas from the pyrolysis of the oil used to produce carbon black. The waste gas consists of H2, C2 H2, CH2, and CO, and is flammable; the other source is the carbon black gas after the carbon black in the gas-solid phase generated during combustion is separated from gas-solid separation in the baghouse dust collector. The carbon black gas, plus the aforementioned waste gas from the pyrolysis of the oil can be collected using a waste gas recirculation method, can be used for drying carbon black in pelletizing and burning fuel for steam power boilers. |
Note 2 | The total internal energy consumption is calculated based on the types of fuels and energy used, including heavy crude oil, purchased electricity, purchased renewable power, biomass fuel, natural gas, and diesel, of which, the process waste gas, self-produced steam, and selfproduced electricity are all products of burning feedstock oils and are not included in the calculation to avoid double calculation of energy consumption. |
Note 3 | The calorific value coefficient of energy conversion is calculated with reference to the coefficient of the table of calorific value per unit of energy products announced by the Bureau of Energy, Ministry of Economic Affairs, in 2023. Because the process conditions of each plant were similar, so Linyuan Advanced’s waste gas composition analysis results in 2019 were adopted for all plants. The calorific value of the process waste gas was 680 kcal/m3. The calorific values of the three plants in China were calculated according to the "Energy Consumption Limits Per Unit of Carbon Black Product", the national emission standard of China. |
Note 4 | Energy intensity is the energy consumption (GJ) per unit of carbon black output (ton); the calculation method is energy intensity = total internal energy consumption ÷ carbon black output in 2023. In 2023, the Group's carbon black output was 348,325 tons, of which 152,734 tons in Greater China, 71,064 tons in India, and 124,527 tons in the United States. In addition to the four production sites in Greater China, Consolidated Resource and the Taipei Headquarters were included in the 2021 data, of which there was no 2021 date for the Taipei Headquarters and its energy consumption was small and insignificant |
Energy intensity of plants in various regions over the past three years
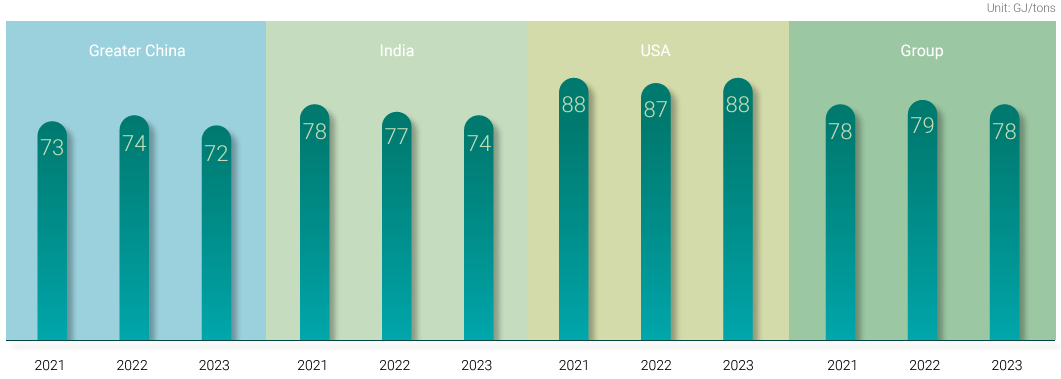
Energy management
CSRC’s energy management is divided into two major directions: energy structure management and energy efficiency improvement. Energy structure management is mainly adjusted toward a circular economy model; for example, the process waste gas recycled is converted into steam to generate electricity for self-use or sale; the construction of a solar power system to increase the generation of renewable energy; and biomass fuel is used to reduce greenhouse gas emissions. Enhancement of energy efficiency aims to improve the electricity efficiency of equipment or reuse thermal energy to maximize the value; for example, the demand for purchased electricity is reduced through the recovery of thermal energy with waste heat boilers, or large equipment is regularly maintained and replaced.
In order to improve energy management performance, CSRC regularly conducts statistics on the energy use status of each operating plant as the basis for modifying the energy policy direction, and the relevant data is checked by the Finance Department to ensure the accuracy of the data. The President and the Assistant Vice President of Finance will participate in such meetings from time to guide the Company's direction for energy conservation and emission reduction.
In 2023, the total power generated in the relevant energy-saving programs in the energy structure management by all operating plants of CSRC exceeded 131,212 kWh, including 911,000 kWh of renewable energy. Among the energy-saving solutions for improving energy efficiency, the use of waste heat boilers to recover thermal energy reduced electricity consumption by a total of 1,305 kWh, equivalent to a reduction of greenhouse gas emissions by 901.94 metric tons of CO2e, and the reduced greenhouse gas emissions are approximately equivalent to the carbon adsorption capacity of 2.3 Daan Parks for a whole year (Note).
Each operating plant will continue to improve its energy management capabilities. In 2023, we began to systematically assess the replacement of fuel oil with natural gas and recycled oil and planned to increase steam and electricity production to effectively reduce greenhouse gas emissions by gradually replacing fuel oil with high-emissions. It is estimated that about 13,469 metric tons of CO2e can be reduced.
Note Based on the fact that 15 metric tons of carbon can be absorbed per hectare of forests per year announced by Council of Agriculture, one Daan Park (25.8 hectares) can absorb 386.4 metric tons of CO2e.
Percentage of group-wide self-generated energy
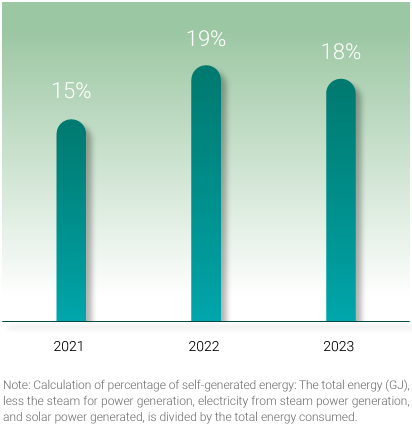
Group-wide energy conservation and carbon reduction projects in 2023
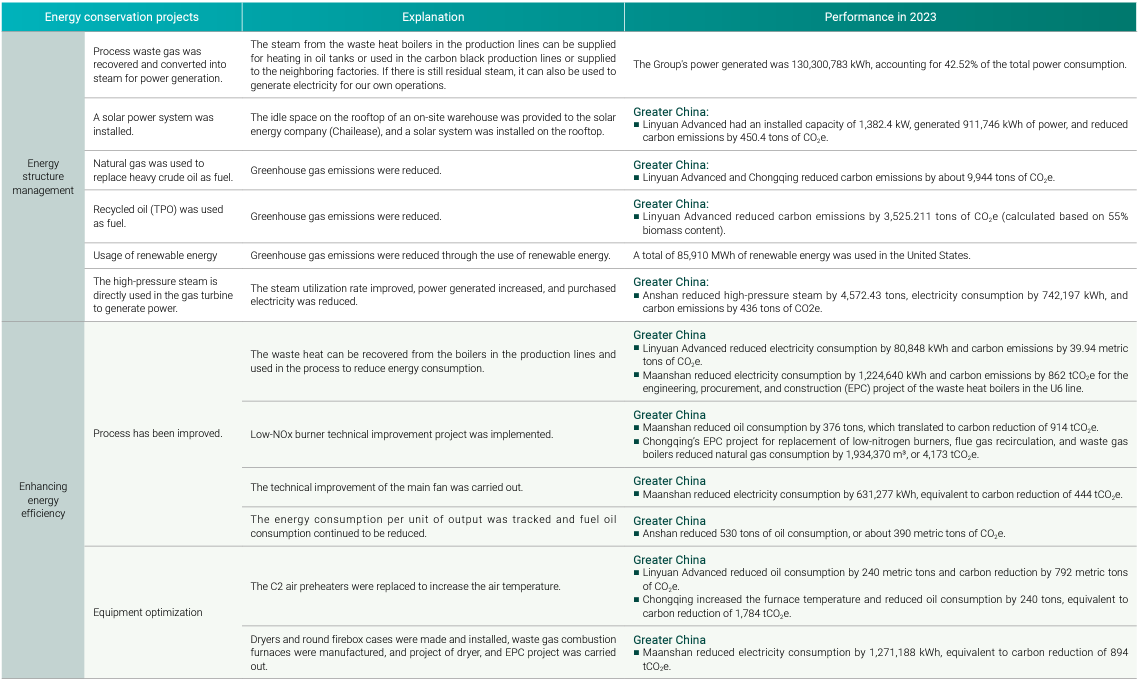

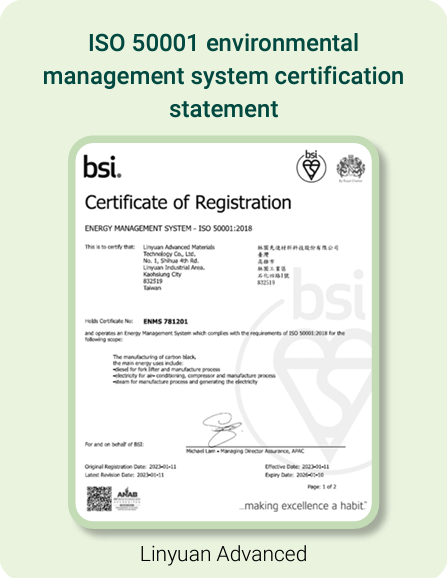
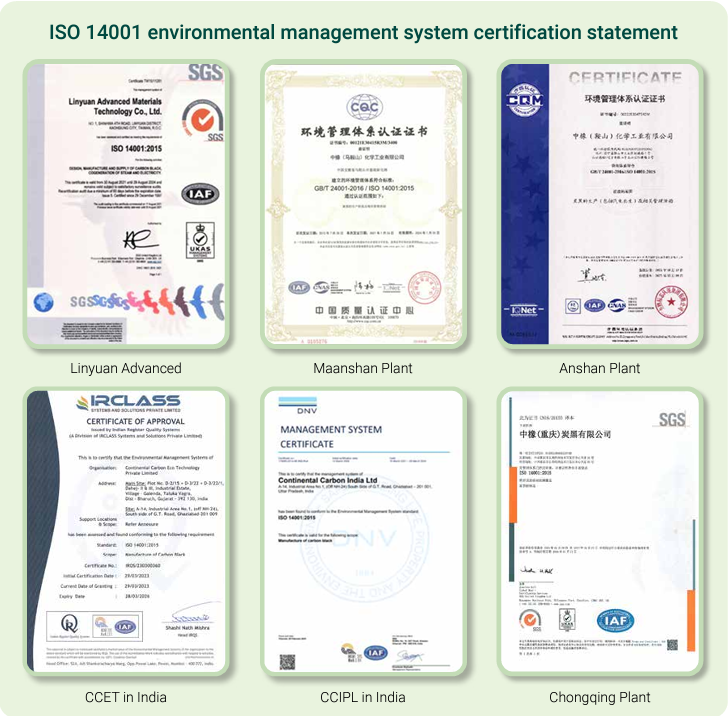
High-efficiency electromechanical equipment was replaced
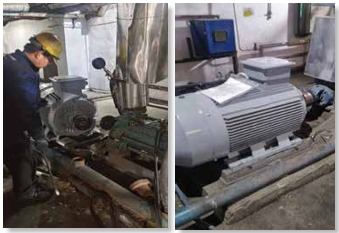
Coverage of production and operation sites adopting environmental sustainabilityrelated ISO management system standards:
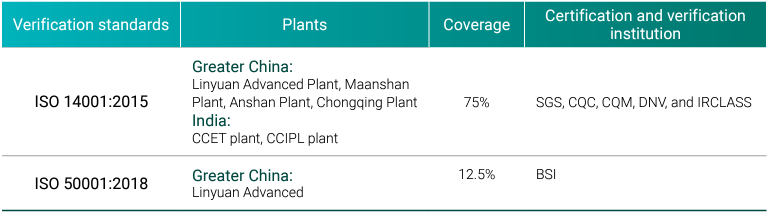
Greenhouse gas inventories
CSRC is concerned about the issue of global climate change. In order to mitigate the impact of the carbon black manufacturing process on the environment, we voluntarily conduct greenhouse gas inventory of each of our plants around the world every year. The accuracy of the inventory data in Greater China has been verified by a third party. To ensure the completeness of the data disclosed, the plants in the United States and India have been included in the scope of disclosure since 2023. Each operating site and building has been tracking, reviewing, and adjusting the inventory results to clarify the performance of production equipment and operating procedures.
In 2023, CSRC's greenhouse gas emissions totaled 1,017,377 tons of CO2e, of which Scope 1 emissions were 909,611 tons of CO2e and Scope 2 emissions were 107,766 tons of CO2e. In the future, we will continue to pay attention to carbon emission trends, supervise and track the consumption of various energy sources, implement sustainable management concept sand energy conservation and environmental protection policies, to reduce the impact of our business on the environment.
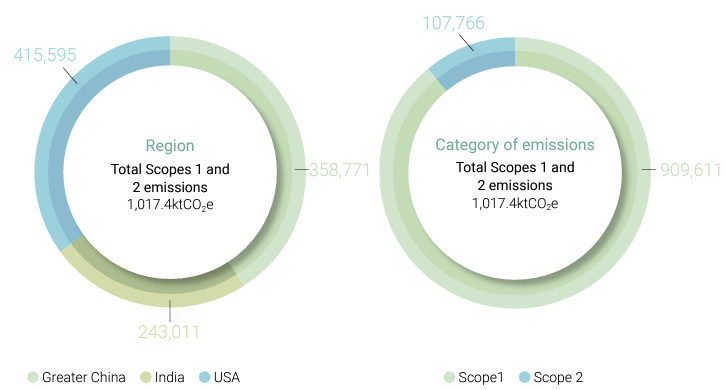
Statistics of GHG emissions in the regions where CSRC operates over the past three years

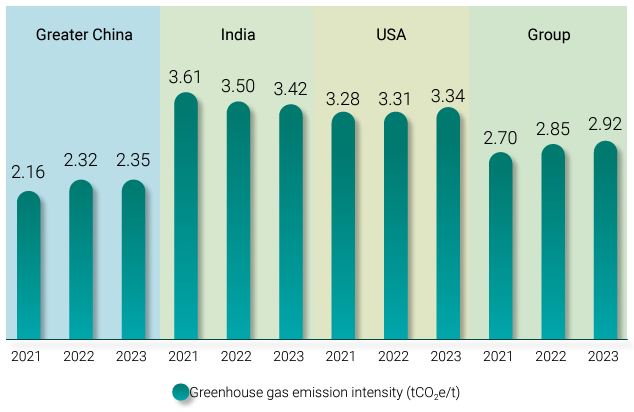
In 2023, the greenhouse gas emissions from plants in the Greater China region were 358,771 tons CO2e, and the greenhouse gas emission intensity was 2.35 tons CO2e/ton. The total emissions were significantly reduced mainly due to the decrease in carbon black production compared to 2022 and the replacement of heavy crude oil with natural gas as a fuel oil. Scope 1 emissions totaled 322,020 tons of CO2e as the main source of greenhouse gas emissions. The items examined in the inventory included waste gas, heavy crude oil, acetylene, diesel, automotive gasoline, slurry, and liquefied petroleum gas (LPG). Scope 2 emissions totaled 36,751 tons of CO2e, with the emission source only from indirect emissions from purchased electricity. The main reason for the increase in Scope 2 was that the total amount of purchased electricity increased due to the decrease in self-produced steam for self-use and sale.
In 2023, the greenhouse gas emissions from plants in India were 243,011 tons CO2e, and the greenhouse gas emission intensity was 3.42 CO2e/ton. This is a significant increase from the total emissions of the previous two years, mainly due to the launch of CCET in India in 2023.
Due to the differences in the carbon content as a result of the differences in carbon emission calculation methods and oil products in different regions, the emissions from the plants in the United States are slightly higher than those in Greater China and India. In 2023, the greenhouse gas emissions were 415,595 tCO2e and the emission intensity was 3.34 tCO2e/ton. The figures significantly decreased from the total emissions in the previous two years, mainly due to the installation of an air quality control system (AQCS) at Ponca and waste gas boilers at Sunray in the United States.
Greenhouse gas inventory verification statement held by each plant in 2023
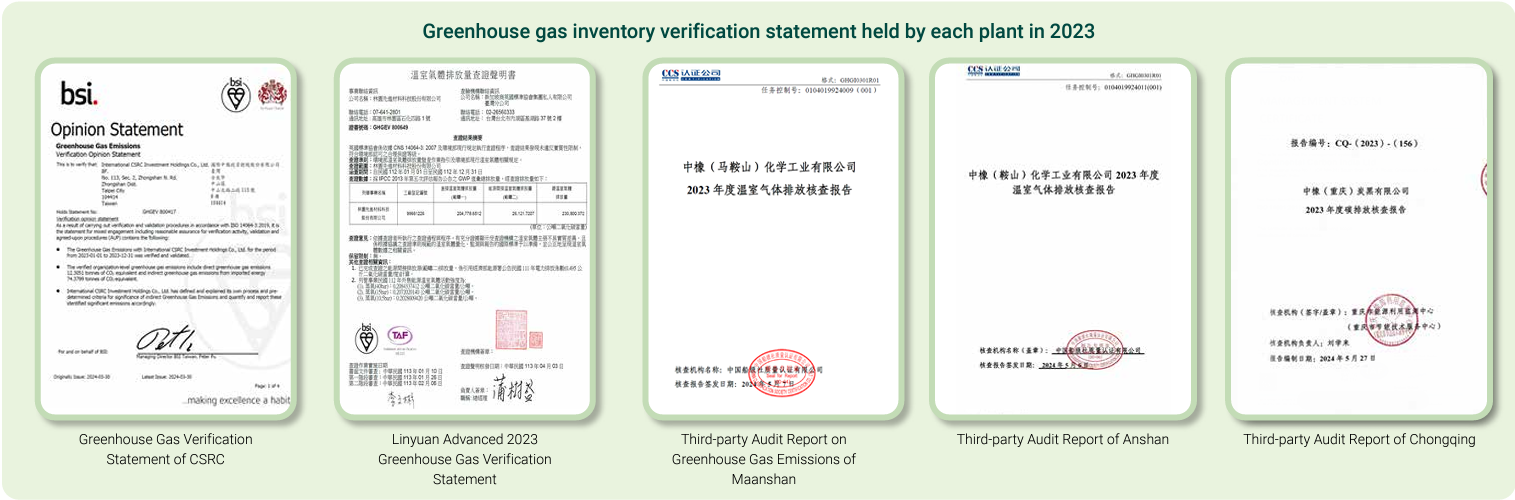
Greenhouse gas management
In the face of global climate change, CSRC is constantly strengthening the Group's climate adaptation and resilience and mitigating greenhouse gas emissions. CSRC conducts a greenhouse gas inventory every year and formulates a greenhouse gas management policy based on the inventory results and then sets reduction targets and draws up measures, while replacing traditional energy with low-emission one to reduce carbon emissions from the process and planning to gradually adopt carbon capture technology. In this regard, we have set the group-wide long-term carbon reduction target for 2030 based on the greenhouse gas emissions and management status of each operating plant, to reduce emissions by 21% compared to the baseline year of 2018. In 2023, the achievement rate was 100%.
To continue to achieve the greenhouse gas emission reduction targets, we have formulated reduction strategies for Scopes 1 and 2 greenhouse gas emissions, respectively. To reduce Scope 1 emissions, the Group regularly improves energy efficiency, evaluates the performance of the improvement to our process equipment, and sets the target of replacing old equipment with new one. We also manage to reduce the use of crude oil by improving production efficiency. Among them, Linyuan Advanced and Chongqing in Greater China adopted natural gas as a fuel to replace heavy crude oil in 2023, and Maanshan is also planning to do so step-by-step. In addition, the plants in the United States use waste gas to produce steam and electricity for on-site use, striving for energy independence and off-site use in the local community. In addition, the plants in India continue to plan the process improvement and parameter optimization of waste gas drying ovens, hoping to reduce the dependence on high-carbon emitting fuels in the future.
In response to the Scope 2 emissions reduction, Linyuan Advanced in Greater China has repurchased the solar panels used by Chailease Finance Co., Ltd. (Chailease) and plans to gradually increase the use of renewable energy in the future. Maanshan's process improvements and adoption of energy-saving equipment (such as the improvement to waste heat boilers in the productions lines and the adoption of energy-saving fans) have led to reduction of purchased electricity consumption by about 487,807 kWh per year in total, equivalent to reduction of 1,734 tons of CO2e. This can effectively save energy and reduce consumption, with economic and emission reduction benefits. Anshan has also replaced equipment with high-energy-efficiency one, and it reduced electricity consumption by about 332,361 kWh, equivalent to reduction of 189 tons of CO2e. The plants in the United States work with local utility providers to purchase renewable electricity. By turning to renewable energy as the cornerstone of the greenhouse gas reduction strategy, we will actively explore opportunities to incorporate renewable energy into the operations in the future.
In order to effectively achieve the goal of greenhouse gas reduction, the Group has established an Emissions Management Team consisting of personnel from the Technical Department, the Safety and Environment Center, and various operating plants. A cross-plant online e-carbon emission monitoring system has been established for plants in Greater China, which can be checked at any time. Regarding carbon emissions, plants in all regions around the world hold regular meetings to review and track carbon emissions and invite each plant to share its carbon reduction solutions and performance with other plants so that they can learn from each other. The monthly and quarterly greenhouse gas emission intensity of the plants in Greater China has been listed as a KPI of the plants. The KPI is linked to the performance bonus to motivate all employees to work together for energy conservation and emission reduction.
To realize the concept of environmental sustainability, CSRC has invested in various environmental protection projects in recent years, including desulfurization and denitrification systems and low-nitrogen burners and has successively built natural gas pipelines in Greater China to replace heavy crude oil as fuel, to reduce carbon emissions. To further promote low-carbon transition, the Group has budgeted greenhouse gas management and regularly reports to the Board of Directors.
Roadmap for low-carbon transition of CSRC
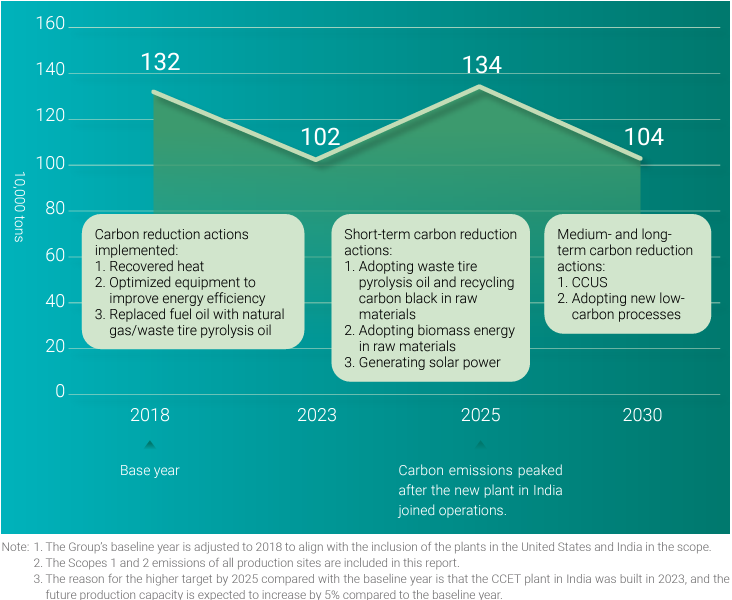
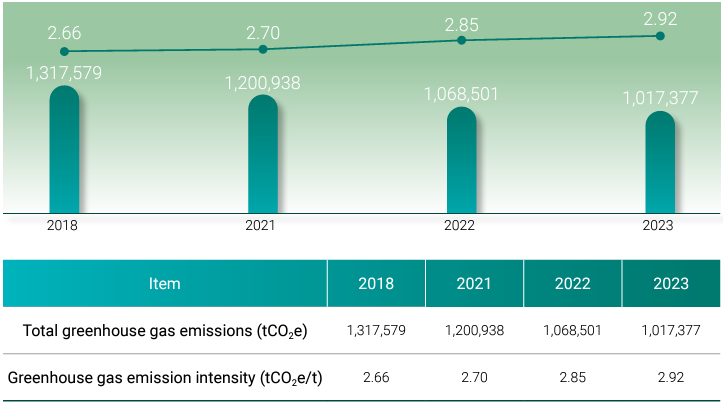
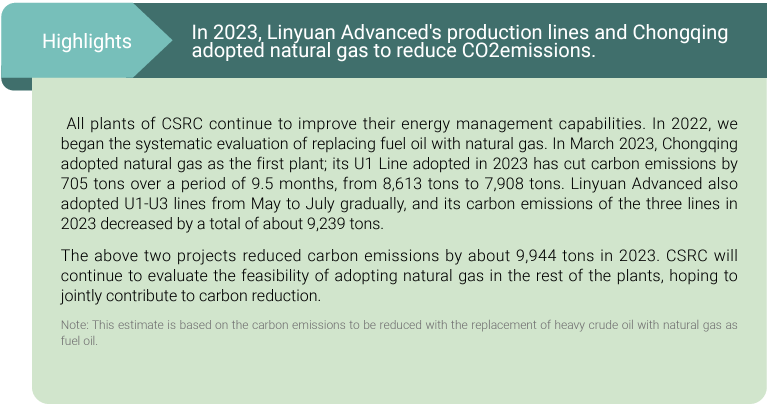