In order to avoid damage to the safety and health of plant personnel or company finances due to hazards such as operations, activities or services and facilities, CSRC uses continuous safety and health hazard identification, risk and opportunity assessments to take appropriate preventive measures, implement necessary control methods, and eliminate hazards. By doing so, we control risks to an acceptable level and improve occupational safety and health performance. This risk management process includes risk identification, risk assessment, risk monitoring, risk reporting and disclosure, and risk response. The process follows ISO/CNS 45001:2018 management system specifications and guidelines for handling; and through regular internal and external inspections, we ensure the execution quality of the process (including the abilities of implementation personnel).
Through our "Hazard Identification and Risk and Opportunity Evaluation Operations", CSRC handles items including risk management policies, risk management organization, risk management processes, and risk management categories and mechanisms, with the purpose of effectively controlling risks arising from business activities. This is to prevent the endangering of safety and health of personnel due to CSRC's operations, activities or services and facilities, causing losses to the safety and health of personnel in the plant or to the Company's finances, and to take early action to address improvement opportunities for occupational safety and health performance.
Risk management process diagram

CSRC has established the "Safety and Health Hazard Identification and Risk Assessment Procedures" according to ISO 45001 standards, actively identifying and assessing hazard factors involved in various operations or services. All evaluators have participated in risk assessment training courses to ensure their capabilities and awareness. The evaluation method can be proposed by factory colleagues (including contractors) or stakeholders of external units to their unit supervisor and reviewed, compiled, and tracked by the implementation task force. Additionally, the establishment of internal and external communication procedures allows employees to participate in incident investigations, hazard risk assessments, and control method decisions. This ensures that all relevant employees, contractors, suppliers, and stakeholders can promptly understand CSRC's occupational safety and environmental policies and the current status of the management system's operational requirements. We formulate routine and nonroutine occupational hazard identification and risk assessment procedures based on the safety and health management system, identifying potential hazards and safety and health risks in each operational plant area and clarifying management strategies through hierarchical control.
The Linyuan Advanced Plant in Greater China categorizes risks into levels 1 to 5, going from large to small severity. Level 1 risks are the most serious and unacceptable, necessitating strict controls. The control methods determined after risk assessment are (a) elimination, (b) replacement, (c) engineering control and work reorganization, (d) use of administrative control including training/signing/warning/ administrative control, and (e) personal protection equipment. The control method adopted according to the assessment shall be considered according to the priority order of (a) to (e), and the most optimal control method shall be determined to reduce the risk to an acceptable level.
In the China area, risks are categorized into three levels based on colors. Every year, the main person in charge of the Company organizes a leadership task force with members to inspect production systems, equipment, facilities, workplaces, and other parts and links according to their respective responsibilities. They conduct a comprehensive and systematic safety risk identification evaluation and collaborate with relevant external experts to assess and demonstrate potential significant hazard sources. For daily risk assessments, the safety risk management and control leadership task force will identify new risk points arising from changes in the environment and production process based on safety production problems found in the comprehensive inspections and daily inspections. The list of risk points will be supplemented and revised by the safety and environmental protection unit. If employees find work to be dangerous, they can refuse the related risky work; and pursuant to Article 32 of the Labour Contract Law and the internal regulations under the “Three Violations Management System,” this is not considered a violation of the labor contract. Employees are also encouraged to report violations and will be rewarded for doing so
The India region also conducts risk assessment and hazard identification for all routine and non-routine operations and implements control measures accordingly, to reduce or eliminate risks. Among them, the CCET Plant categorizes incidents into four levels: minor, moderate, major, and natural disaster levels, each with specific handling protocols. Regular internal and external audits are conducted at the plant to ensure personnel adhere to procedures or SOPs for risk assessment and hazard identification, thereby preventing any process gaps. If a work item is dangerous, workers also have the right to refuse or interrupt the work to ensure worker safety.
In the US region, workplace hazard assessments are conducted and Job Safety Analysis (JSA) is developed as a preventive guideline. The occupational safety unit is responsible for comprehensive development and maintenance, with reviews at least every three years and updates as needed. Employees or contractors are authorized to exercise Stop Work Authority (SWA) and immediately report unsafe conditions.
Regarding risk management with contractors, CSRC aims to collaborate with them, emphasizing quality and scheduling. We require external contractors to sign agreements ensuring their understanding and cooperation with the company's risk notifications. The implementation focuses primarily on labor health, hygiene and safety, environmental and ethical standards, labor rights, and other aspects. This is to prevent and mitigate significant occupational health and safety impacts related to the Company's operations. This ensures that excellent suppliers can provide high-quality and stable raw materials, while engineering contractors can offer professional construction or supplement factory construction manpower shortages.
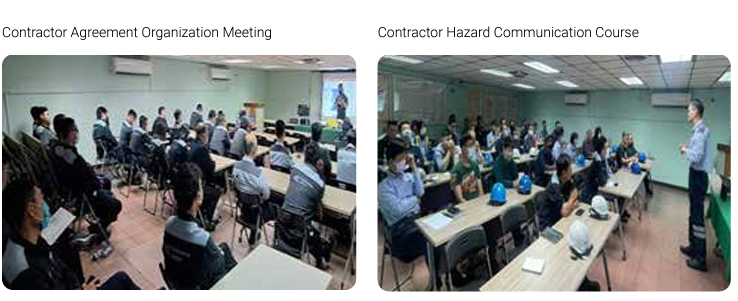
Process Safety Management (PSM)
To reduce CSRC's impact on safety and the environment and effectively mitigate process incidents, the Linyuan Advanced Plant in Greater China began implementing Process Safety Management (PSM). This implementation proceeds gradually through planning, execution, inspection, and improvement, enhancing the safety management of process operations. We aim to establish and enforce a factory safety culture and system, involving everyone from senior managers to employees and from equipment to personnel. The implementation of the overall plan is divided into two stages (36 months in total). The first stage involves system introduction, and the second stage focuses on deepening system and technology enhancements, with plans for gradual implementation in other regional plants.
Promotion of Process Safety Management (PSM)
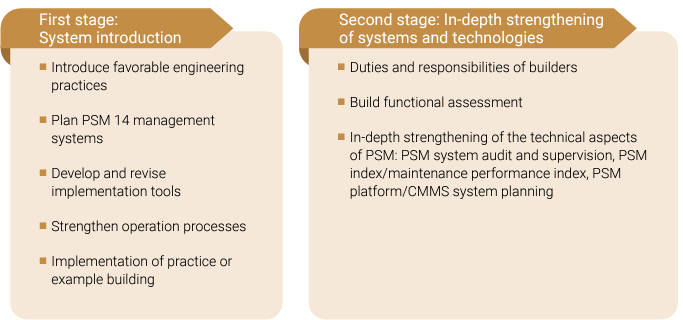
Key risk items and response measures at each operational site are as follows:
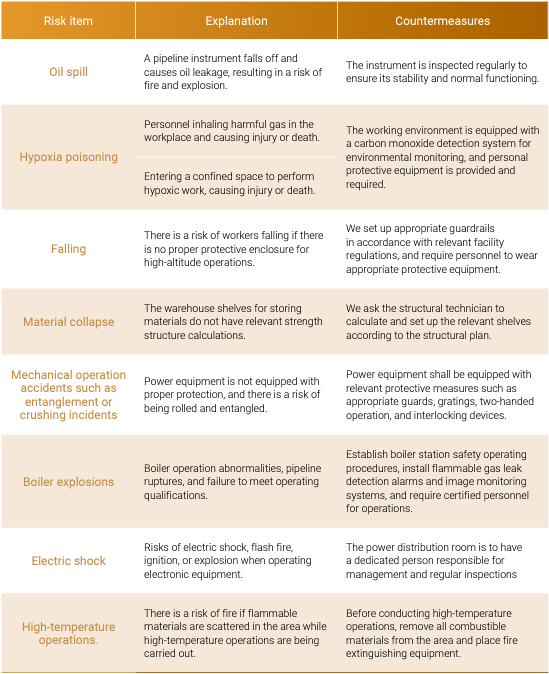
In order to protect the health of employees and prevent the occurrence of industrial safety accidents, each operational site of CSRC complies with laws and regulations to formulate chemical management guidelines to reduce occupational safety risks caused by hazardous chemicals.
The Linyuan Advanced Plant in the Greater China region adheres to Article 10 of the Occupational Safety and Health Act and Article 17 of the Hazardous Chemical Labeling and General Knowledge Rules in making its safety and environment office responsible for formulating a Hazard Communication Plan and updating it in due course. All China-based facilities comply with the regulations of the Law of the People’s Republic of China on the Prevention and Control of Solid Waste Pollution. Pollution from oil and chemical usage is controlled and managed. Chemical Management Measures are established at each facility in accordance with regulations to ensure workplace compliance with occupational safety requirements. This enhances employees' awareness of potential hazards from hazardous chemicals, preventing harm. Fixed and portable alarms are installed throughout the facilities to monitor toxic gas levels and ensure personal safety. Additionally, third-party monitoring is regularly conducted on labor operational environments, focusing on chemical and physical factors
In India, chemical names are labeled according to local regulations. Material Safety Data Sheets are provided in English and local languages to ensure safe chemical handling and employee safety. Hazardous substances are managed in accordance with India's 1948 Factories Act, with internal work guidelines and relevant training provided to employees and contractors. In the United States, the Chemical Hygiene Plan and the Spill Prevention, Control, and Countermeasure (SPCC) Plan are developed based on OSHA procedures.
Each production site manages chemicals according to the following key points:
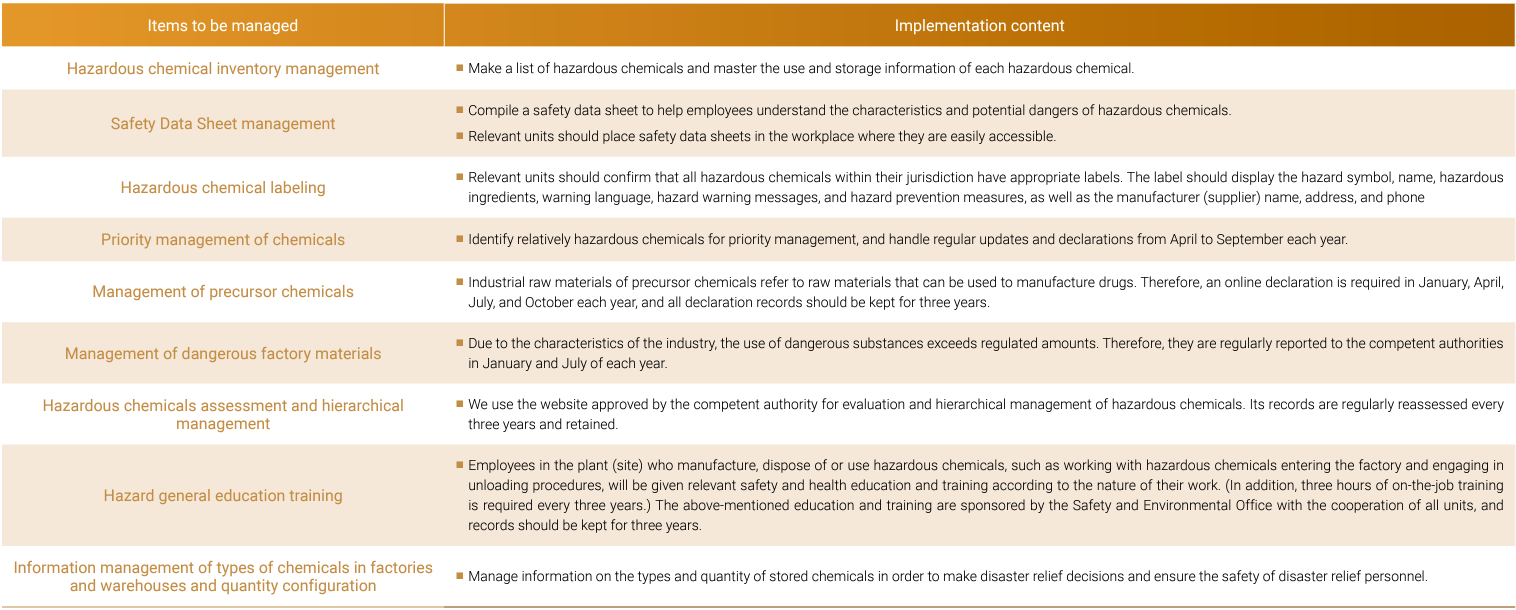
Each operational site formulates key management items for chemical management as follows:
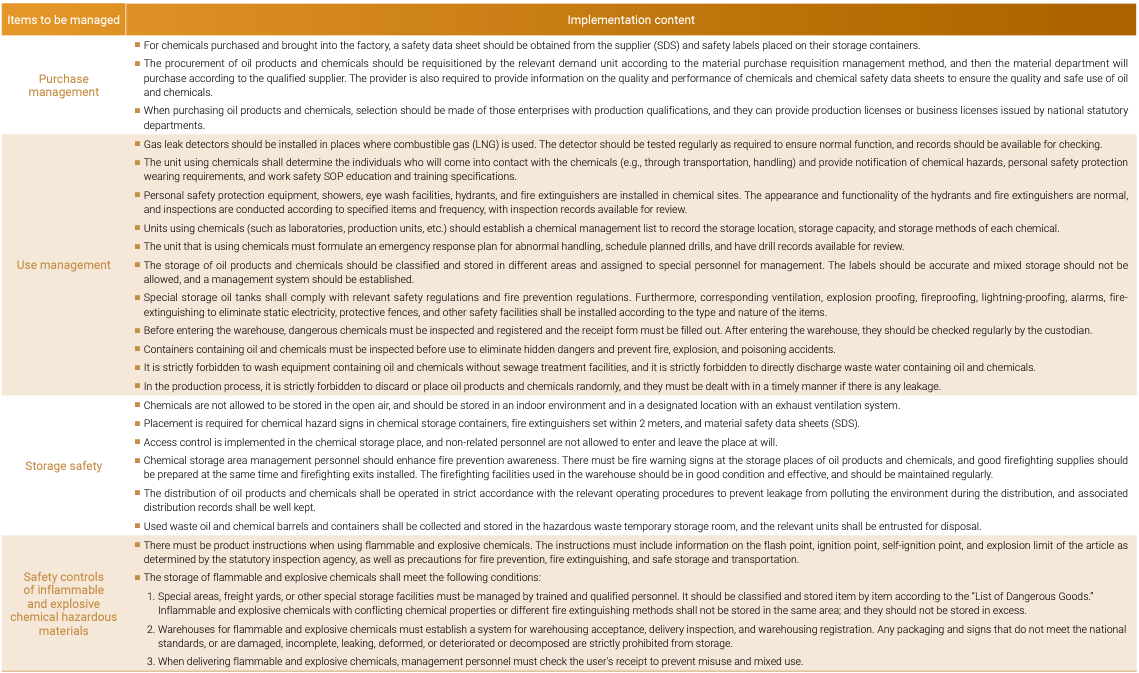
CSRC posts color markings for equipment paint pipelines in plants of each region and reminds employees to wear protective equipment.
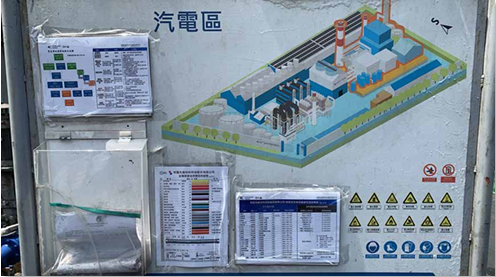